The Creative
To guarantee an adequate safety level for pressure equipment, the European Pressure Equipment Directive prescribes that appropriate design calculations must be performed to establish the strength of the pressure equipment concerned. SAMSON was certified and approved as an additive manufacturer of semi-finished products in 2021. Based on a certified quality management system, we are capable of manufacturing pressurized parts of austenitic stainless steels using the laser-based powder bed fusion of metals (LB-PBF-M) method.
In-process inspection
SAMSON continuously verifies the minimum material properties through non-destructive testing on the products themselves and destructive testing on specimens printed along with the products. On request, testing is documented for our customers.
Quality guaranteed
SAMSON has put in place a comprehensive quality assurance system tailored to the new additive manufacturing method, including incoming inspection for the powder feedstock, qualification of the manufacturing parameters and staff as well as in-house lab testing.
Compliance achieved
SAMSON was certified by TÜV SÜD Industrie Service as an additive manufacturer of semi-finished products based on our compliance with EN 13445-4 and the general safety requirements laid down in the Pressure Equipment Directive.
Additively manufactured parts
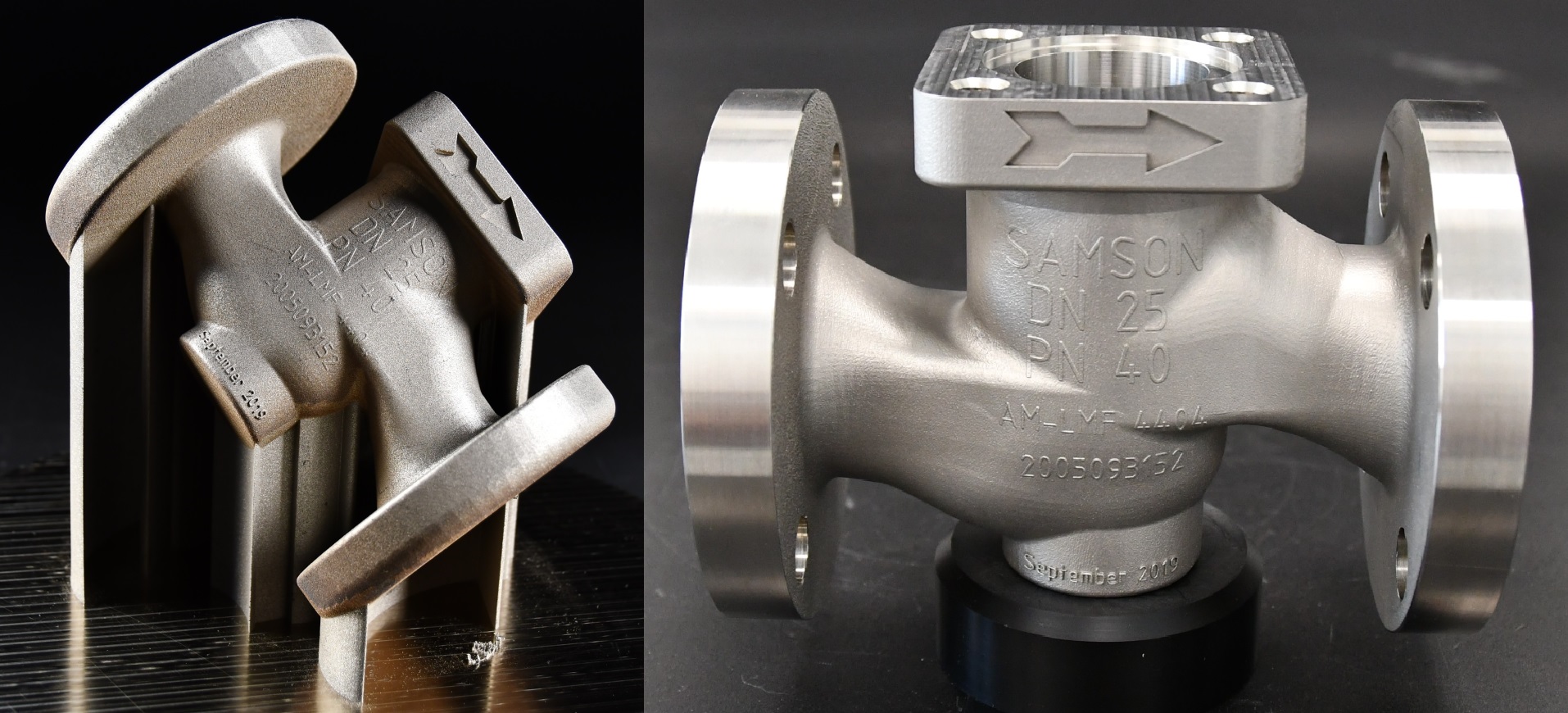
ACHEMA 2022
Prime product quality
-
Prototype construction
Prototype construction plays an important role in product development. It provides essential information for implementation in series production, particularly when designing complex parts. In addition, prototyping focuses on future manufacturing methods. In SAMSON's ROLF SANDVOSS INNOVATION CENTER, traditional tools machinery as well as CNC machining centers are used for prototype construction. Additive manufacturing of plastic parts based on 3D design data is already possible. Implementing additive manufacturing also for metal and ceramic materials is planned.
-
Materials engineering
Prototype construction plays an important role in product development. It provides essential information for implementation in series production, particularly when designing complex parts. In addition, prototyping focuses on future manufacturing methods. In SAMSON's ROLF SANDVOSS INNOVATION CENTER, traditional tools machinery as well as CNC machining centers are used for prototype construction. Additive manufacturing of plastic parts based on 3D design data is already possible. Implementing additive manufacturing also for metal and ceramic materials is planned.
-
Digital infrastructure
More than 200 test instruments are operated in the ROLF SANDVOSS INNOVATION CENTER based on a fully integrated measuring and automation system. Thanks to the digital infrastructure, it will be possible to perform real-time tests including simulations of various plant and operating conditions as well as compile and analyze the collected data. A modular communication infrastructure helps ensure that the smart SAMSON products are compatible with all common process control, engineering and asset management systems and that they can be connected to cloud computing systems. With this setup, research and development into shifting smart features to the field devices to achieve decentralized control can be intensified.
-
EMC and device safety
The electromagnetic compatibility and safety of SAMSON products is verified in the CE Lab. Tests at frequencies up to 18 GHz can be performed in an anechoic chamber for radiated interferences and emission measurements. Stations have also been set up to test electrostatic energy and conducted interferences, like they occur when the voltage drops or lightning strikes. Based on the tests performed in the CE Lab, SAMSON can document the required CE compliance of products.
-
Life cycle tests
SAMSON products are characterized by their long service life, even if they are operated in the most adverse process and ambient conditions. To achieve this durability, individual parts as well as complete control valves are subjected to life cycle tests in the ROLF SANDVOSS INNOVATION CENTER. The tests cover the specimens' chemical, thermal and mechanical resistance as well as their flow characteristics and suitability for specific climate conditions. The available test facilities include various simulation and climatic cabinets, ovens and flow test benches.
-
Fluid mechanics
We are committed to understanding and controlling the flow of media. Process media in all possible conditions, such as liquids, gases, vapors, multi-phase flows and even liquids containing solid particles, can be simulated on different test benches in the ROLF SANDVOSS INNOVATION CENTER. In the Flow Labs, valves in sizes up to DN 500 (optionally up to DN 1000) can be subjected to flow, acoustic and function tests, they can be calibrated and their operation under specific plant conditions can be simulated.
These industries work with our solutions











